Table of contents
Both in workshop and office environments it is important to set up and design workspaces that are suitable for the body. By doing so, you can reduce the risk of occupational illnesses and accidents. Through the sensible planning and implementation of ergonomic measures, employees and equipment can be looked after in an appropriate way
To achieve workplace comfort and optimal ergonomics, you need to consider the workplace holistically. As such, the following need to form part of your workplace comfort strategy:
- Design and arrangement of work equipment
- Lighting in the workplace
- Indoor climate
- Work organisation
In the following guide, we will provide more information about the ergonomics of workbenches and production workspaces, the correct ergonomic equipment for industrial trucks, as well as office and computer workplaces. To ensure that work areas are designed in an optimal way, our guide also shows you how to include factors such as body size and strength in your strategy.
Are there legal regulations for ergonomics in the workplace?
The UK Health and Safety Executive (HSE)stipulates that employers must protect the health and safety of their workers and others who might be affected by what they do. This is stipulated under the Health and Safety at Work Act. In addition, the Management of Health and Safety at Work Regulations require employers to assess the risks to the health and safety of workers.
In order to comply with regulations, you must provide your employees with an ergonomic workplace. The regulations are in place to secure both the ergonomic adaptation of the workplace to the employee and the preservation and increase of competitiveness in UK businesses.
Ergonomics in the workshop
The ergonomic design of your workshops is not set in stone but is part of an ongoing and adaptable process. In order for employees to be able to work ergonomically, healthily and safely on production lines, at workbenches, or when operating production machines, the ergonomics of workshops should be checked regularly and adapted if necessary. Our 7-question list can help you achieve best practice in this area.
1. Are the chairs and worktables optimally adjusted?
Ergonomic desks, and chair heights that can be adjusted, are ideal for you and your employees. They enable the user to adopt a comfortable posture that is easy on the back while working. Especially in office work, a chair should preferably have a range of adjustment options to enable a dynamic sitting posture and meet ergonomic requirements.
This means:
- The seat height is adjustable
- The seat depth and seat width are adapted to the employee (at least two-thirds of the thighs should be on the seat surface)
- The backrest is individually adjustable in height and inclination
- The spine is well supported
- The chair is stable and cannot tip over – five castors are recommended
- The office chair has rounded front edges and good upholstery
- The armrests are adjustable in height and depth.
The optimum ergonomic working height should be at elbow level or slightly below when the thighs are about a hand’s breadth from the lower edge of the ergonomic desk. For this purpose, the worktable should also ideally be height adjustable.
2. What is joint-friendly equipment?
In the office, ergonomic computer workstations should be easy on the wrists, elbows and shoulders. In the workshop, ergonomically shaped and cushioned anti-fatigue mats help to relieve strain on the body during long periods of standing. Ergonomic safety shoes also reduce the strain on knees and ankles.
3. What lighting conditions are optimal for an ergonomic workplace?
Good lighting conditions are essential in the workplace and have a positive effect on mental health, as well as productivity and safety. To ensure ergonomic working conditions, workplace lighting should be a variable mix of daylight, indirect and direct lighting. Ideally, the intensity of the lighting should be 500 lumens. Lamps should be installed in the line of sight so that they do not dazzle. In addition, workplace lighting must also be flicker-free.
4. Are the screen and keyboard ergonomically adapted?
These days lots of work is done on a computer – even in a workshop environment. Computer workstations have become part of everyday work. The following aspects are important when selecting and setting up an ergonomic monitor:
- Screen distance about 60-80 cm depending on size
- Upper edge of the screen at eye level
- Screen positioned to the front of the field of vision
- Set up parallel to the window front
- Display is flicker-free
- Characters on the monitor are easy to read
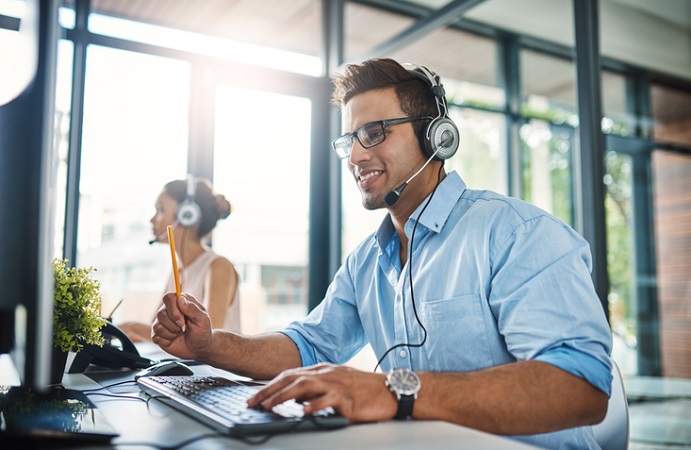
There are also ergonomic workplace design criteria for the keyboard:
- It should be possible to place the heel of the hand about 5-10 cm in front of the keyboard
- The inclination of the keyboard should be about 5-11°
5. What are the ideal air conditions and temperature in the workplace?
The indoor ambient environment depends on good humidity. Room air that is too dry can irritate the mucous membranes and respiratory tract. The guideline value for good air humidity is about 40 to 60 percent. To achieve this value, humidifiers or water containers can be integrated into the room. The recommended workplace temperature is around 22˚C. Also remember that sun protection may be essential, especially in the summer months.
6. Is there sufficient freedom of movement?
Freedom of movement is also important for ergonomics in the workplace. A generous arrangement and design of the workshop or office ensures that working materials and aids can be easily reached. If employees have enough space in the workshop to handle machines and between workbenches, work processes can be carried out not only ergonomically but also safely.
7. Have you created an awareness of ergonomics in the workplace?
Once all measures for ergonomics in the workplace have been practically implemented, it is important to make employees aware of regularly reviewing their work processes and habits. Workplace ergonomics cannot just be limited to the inventory and the environment. Employees must be encouraged to actively contribute to a successful workplace design on a daily basis.
The importance of correct working height for ergonomic design
An appropriate workbench height prevents incorrect posture when working in a standing or sitting position. With correct ergonomic working height, it is possible to perform all activities with a healthy and correct body posture.
Good ergonomic workplace practices when standing at worktables, workbenches and machines should be:
Activity (standing) | for women (165 cm height) | for men (177 cm height) |
---|---|---|
Fine work | 95-105 cm | 100–110 cm |
Skill work | 85–90 cm | 90–95 cm |
High-force work | 79–85 cm | 75–90 cm |
Ergonomic work equipment that is height adjustable makes it possible to provide each employee with a suitable workplace.
You can also ensure that ergonomic workplace practices are observed when lifting and carrying materials and goods with the support of a forklift truck. At Jungheinrich PROFISHOP you can choose from stacker trucks and pallet trucks to bring goods to an optimum height, compensating for height differences when loading and unloading or picking.
Workplace ergonomics for forklift trucks and pallet trucks
The ergonomics of forklift and pallet trucks have a great effect on the operator. The working posture for the respective operating and steering functions can affect physical strain and fatigue. Therefore, comfortable and body-friendly posture should be the aim of ergonomic workplace design.
The operating and steering elements of the equipment are the key ergonomic interfaces. That’s why many modern industrial stacking and lifting trucks are adapted to the physical requirements of the operators.
Ergonomic workplace design for industrial trucks with pedestrian operation
With pedestrian operation, steering and operating functions are triggered simultaneously. Walking is a natural human movement and has a positive effect on the body. However, pulling loads in pedestrian mode requires a lot of energy, especially when transporting over longer distances. For this reason, industrial trucks without electric drive, such as hand pallet trucks and scissor lift trucks, should only be used on short transport routes on level roadways.
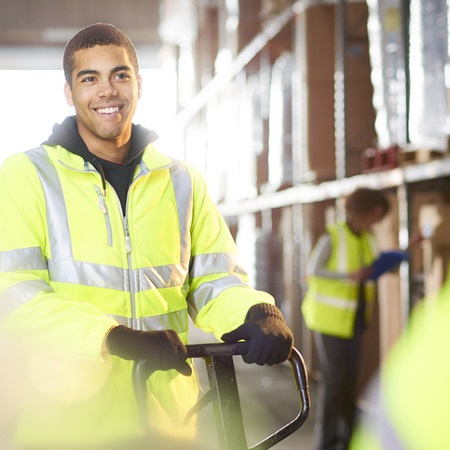
An important aspect of ergonomics for pedestrian operation is the shape and length of the tiller. In the driving position, a comfortable arm position should be possible and sufficient distance between the vehicle frame and the operator should be ensured during all manoeuvres. In addition, an ergonomic design of the tiller handle and a casing for the lift-drive-lower functions for both left- and right-handers ensures comfortable handling in everyday work.
In many electric pallet trucks and electric stacker trucks, the operating elements are also contained in the ergonomic tiller and are optimally accessible with the index finger and thumb. This makes it possible to work in an ergonomically correct way, without having to reach around or overextend. In an ergonomically correct and modern industrial truck, the tiller should also be the control element for the brake and should automatically move into the brake position. An additional function for trucks with an electric motor drive is the crawl speed button. This enables ergonomic manoeuvring in confined spaces.
Ergonomic working with standing rider operation
In standing ride-on mode, the operator is carried on a platform. The ShockProtect feature has an ergonomic effect on the spine and joints, absorbing all shocks during use. The following features also ensure correct ergonomic standing operation in the workplace:
- Industrial trucks with foldable stand-on platform: A foldable operator platform allows you to switch between pedestrian and rider operation. A non-slip rubber coating ensures safe standing, and an additional folding sideguard keeps the operator securely on the platform when cornering. Stepless, jerk-free pulse control in ride-on mode minimises jolts and also ensures the necessary work safety.
- Industrial trucks with fixed stand-on platform: The fixed operator stand-on platform limits the operating and steering functions between the pick and delivery points on horizontal order pickers. The driver’s platform should be set up so that it does not restrict the freedom of movement. Access to the platform from both sides is recommended. In addition, rubber buffers should support the driver’s firm footing.
Trucks with seated rider operation
Seated rider operation is mainly found on counterbalance trucks. For optimal ergonomic operation, steering should be smooth both when the truck is empty and when loaded. It is recommended that the controls are in the driver’s field of vision and operating and holding the controls should require minimal effort. There must also be sufficient clearance between the hand controls to allow unhindered handling with work gloves.
Industrial trucks with seated passenger operation are available with front seat or side seat positions. A side seat is recommended when reversing. The driver’s seat should be flexibly adjustable for this purpose. Hydraulically suspended seats and backrests relieve the spine when the ground is uneven and must also be individually adjustable. Sufficient free space in the driver’s compartment allows the driver to change position ergonomically, even while sitting.
FAQ for workplace ergonomics
Ergonomics (ergon = work, nomos = law/rule) comes from the Greek and technically relates to the laws of work. The field includes the optimal design of interfaces between man, machine and environment. The aim of ergonomics in the workplace is to create optimal working conditions for employees through more suitable design and equipment.
Both in the workshop and in the office, it is important to set up the workplace ergonomically and to design it in a way that is suitable for the body. This helps to create optimal working conditions for your staff. In this way, the physical and mental health of the employee is protected, and the risk of occupational illnesses and accidents is reduced.
Depending on the workplace, different areas have specific ergonomic considerations. In a workshop or warehouse, there are different criteria to those in an office or other work environment. In addition to factors such as the design and arrangement of work equipment, lighting and room climate can also play a central role in workplace ergonomics.
Please note: The regulations mentioned above represent only a selection of the most important legal requirements. Please refer to the listed organisations and directives for more detailed information. If in any doubt, consult experts or contact the relevant regulatory authorities.
Image source:
© getty – alvarez
© getty – PeopleImages
© getty – sturti