Table of contents
Without the use of pallets, many modern warehouse or logistics processes are hard to imagine. A wide variety of goods are stored and transported using palletisation – from small, stackable packaging units to large, bulky goods.
Special care must be taken when loading pallets. After all, unevenly distributing goods or inefficiently securing them can result in damage during transit or even avoidable workplace accidents. In this guide, we will cover everything you need to know in relation to palletising including types of pallets available and what palletising techniques you should be adopting for your business.
What is the purpose of palletising?
In logistics, the term palletising encompasses all processes in which goods are loaded onto pallets for transport or storage. The aim: Combine raw materials or products into packaging units that are as uniform as possible, so that even larger quantities can be transported and stored efficiently using pallet trucks and forklifts or similar equipment.
The palletised goods form a stable unit that can make the most effective use of available storage space. In palletised form, goods are also far better protected against storage and transport damage compared to individual goods.
Advantages of palletising at a glance:
- More efficient loading and unloading of goods when using industrial trucks
- Stacked goods enable faster transport and flow of goods within the warehouse
- Optimal use of available storage space by stacking goods and pallets
- Increased safety for employees and greater protection for stored goods
Pallet types and dimensions
Transport pallets are available in different dimensions and materials depending on the requirements of the goods or storage space. To be able to calculate how many items fit on a pallet during palletising, exact pallet dimensions must be known. And to save on shipping costs and packaging material, the use of pallet space should be maximised. The most widely used pallets are the proven wooden Euro pallets, the dimensions of which are specified in the EU standard 13698 as follows:
- Standard dimensions (also called Euro dimensions): 1200 mm x 800 mm
- Half-Euro dimensions: 800 mm x 600 mm
- Quarter Euro size: 600 mm x 400 mm
Another frequently used dimension is the so-called Industrial Dimension, typically used for larger goods, with a length of 1200 mm and a width of 1000 mm.
The Euro dimension is often considered in the design of transport aids, storage systems and pallet racks. It is so widely used that plastic pallet types, often made from recycled materials, as well as other versions including stronger metal pallets and specialised pallets are also available in the standard Euro size. This not only allows you to make the most of your warehouse space but also makes it easier to establish joint logistics with suppliers and customers – important steps for optimising your warehouse processes.
Though the Euro pallet is most popular, there are alternatives available. Which one is best for you depends on your operations and the goods you wish to transport. In some industries, strict hygiene regulations necessitate the use of germ-free, disinfectable materials, while other industries might demand the use of particularly large or reinforced pallets.
The right palletising technique
When it comes to optimal palletising, two important factors need to be considered – the even distribution of load and the safe securing of goods. The load should not have room to shift during transit. Nor should it be too tightly compressed, which risks damaging packaging or even the goods themselves. Once the correct pallet type has been selected, it is now particularly important to ensure uniform loading and compliance with permissible load capacities. Here is how to do it:
- Distribute load evenly across the pallet
Place items on the pallet in their packaging or in stackable containers, cartons and boxes that are tailored to the dimensions of your chosen pallet type. Avoid overhangs or empty spaces. If empty spaces cannot be avoided, place the load in the centre. If necessary, you can build in gaps in a purposeful manner, ensuring the stability of the load is not compromised.
In the case of protruding loads, check whether transport is still permissible in accordance with relevant regulations, and that your storage system offers enough space. Always distribute the centre of gravity evenly and close to the ground – never too far to one side or too high within the stack. This is especially important while operating a forklift to ensure a safe working environment. - Applying palletising best-practices
To stack goods safely, there are two common techniques:
If stacking in columns, place the boxes side by side, layer by layer, following a uniform pattern. This can be done quickly and efficiently but also results in individual towers that are not connected to one another. This makes the columns less stable than a single, interconnected stack.
Interlock stacking involves creating a staggered pattern between each layer of goods. Once the first layer of the pallet is filled, start the second layer by placing boxes in the centre of two goods on the lower level. This arrangement resembles that of a brick wall and ensures a more stable load. - Securing the goods reliably
After palletising, you need to secure the individual units to form a compact load unit.
For small-scale goods, securing the load with stretch wrap is suitable. Film can be applied either manually or with the help of a stretch machine. Larger goods can be secured effectively with the help of lashing straps.
For securing particularly heavy goods, you can combine several securing methods alongside Pallet Collars to prevent movement. These are also recommended for palletising irregularly shaped goods.
The permissible load capacity plays an important role in palletising. Always keep in mind that it is not only the load-bearing capacity of the pallet itself that needs to be considered. During storage, you must also take into account the safety-relevant regulations for pallet racking, as well as the load capacity of forklifts and pallet trucks.
Common palletising errors
Most palletising mistakes occur during the stacking of the boxes or during load distribution. Once a pallet is fully loaded, the first thing you should do is check whether you have a regular rectangle shape with uniformly straight sides.
In the case of column stacking, goods have a tendency to fan out in all directions or slide to one side as the height increases. A bulbous shape indicates that there are too many layers on the pallet. The lower goods might be compressed under the excessive load.
If this happens you can correct the alignment or remove a few layers from the pallet before securing the load. Never try to correct the shape with the aid of tension straps or stretch film. Deformations are a sign of instability, which even good load securing cannot always compensate for.
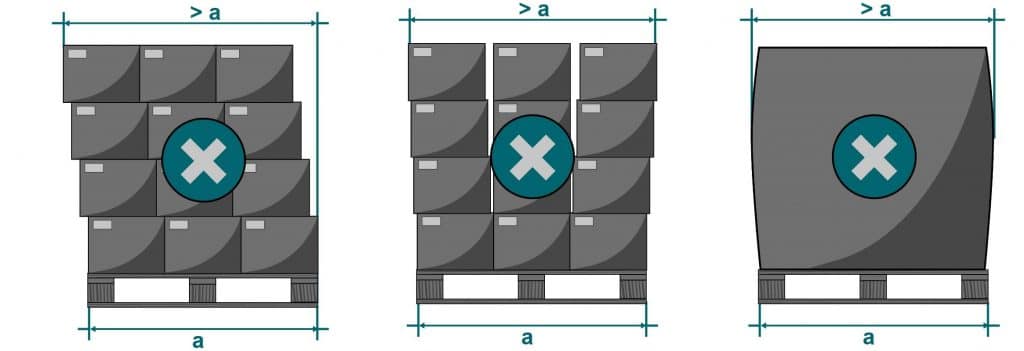
Manual or automatic palletising?
For smaller-scale operations, warehouse or company employees might be able to complete the palletising by hand. However, if your company regularly ships large quantities of the same products, it makes sense to adopt automatic palletising to save time and money in the long term.
Automatic palletisers are available to fit a broad range of different requirements – from programmable pallet-loading robots capable of loading individual items, to large loading stations that place a complete stack of goods on the pallet.
Choose from the following mechanical palletising aids:
- Pallet loading stations enable you to automatically transfer complete stacks of goods to pallets, saving considerable time and manpower.
- Layer palletisers combine crates, boxes or other containers into individual layers and place them on a pallet.
- Collaborative robots (‘cobots’) reduce the need for additional manpower by taking over specific steps in the loading and unloading process. While traditional linear robots load pallets in a specific pattern, palletising robots can be programmed to execute different packing parameters based on your specific requirements.
Some systems can even handle the de-palletising of incoming goods and can be combined with existing conveyor belt technology for goods distribution. Such central palletising, in which a wide range of tasks are completed by a single machine, is particularly beneficial for large warehouses and production companies. This automation of warehouse logistics ensures that all processes are optimally interdependent. Alternatively, using several palletising robots (with each performing a limited number of specific tasks) is referred to as decentralised palletising. This method allows greater flexibility and makes it easier to optimise individual processes.
FAQ about palletising
In the logistics industry, the term palletising encompasses all processes in which goods are loaded onto pallets for transport or storage. The meaning behind palletising is to combine raw manufacturing materials or products into packaging units that are as uniform as possible so that even larger quantities can be transported efficiently with pallet trucks and forklifts. The palletised goods form a stable unit and, with the aid of professional load securing, are better protected during transit and easier to store.
When it comes to palletising, it is vitally importantto distribute the load evenly on the pallet and properly secure it. You can stack the goods in columns or interlock them. Stretch film is suitable for securing smaller goods. For palletising bags, large goods, or irregularly shaped items, it is best to use robust pallet attachments.
Automatic palletisers are available to fit a broad range of requirements – from programmable robots that load individual items to large loading stations that place completed stacks onto a pallet. Some systems can also support de-palletising and handling of your incoming goods and can be combined with conveyor technology for goods distribution. Such complex solutions are particularly beneficial for large warehouses and production plants, where the automation of warehouse logistics ensures that all processes work together in an optimised manner.
Image source:
© Jungheinrich AG