Table of contents
Until recently, 3D printing houses sounded like science fiction, but it is now opening up entirely new possibilities for the construction industry. The 3D printing construction process is now so advanced that it can be used to print habitable buildings. The technology is still in development but has already been successfully applied in various projects. In this guide, you will learn how a house is built using a 3D printer and what opportunities and challenges this new technology offers.
Differences between 3D printed homes and conventional construction methods
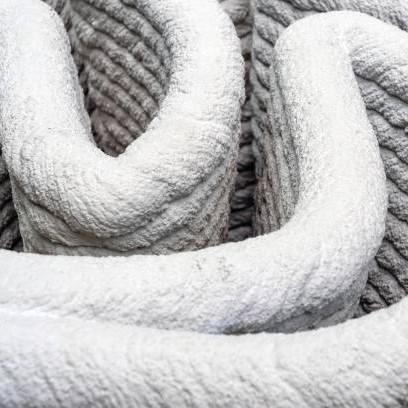
A printed house is fundamentally different from a conventionally built building but exactly how do they differ?
- The different aesthetics of the walls are recognisable immediately, because the layer-by-layer application of the material is not only visible during the printing phase, but also in the finished product
- The curved shape of the walls can also be characteristic, depending on the style in which the building is constructed
- However, there are also special features of a building created using a 3D printer that are not immediately obvious. These include, for example, the fact that a 3D printed house is created without formwork. Conventional concrete components are poured into a formwork that holds the liquid mass until it is dry and dimensionally stable. This is not necessary with 3D homes. The material hardens quickly and is very high strength, so that no formwork is required.
The speed
One of the biggest differences between conventional construction and 3D printing construction is the speed. Whereas, in conventional house construction, brick is usually laboriously placed upon brick by human hands, a 3D construction requires only two trained employees to monitor the technology and provide assistance when necessary. The printing speed varies depending on the printer model and ranges from about 25 centimetres to one metre per second. The construction process is further accelerated by the fact that several work processes can already be carried out during printing. Secondary trades that normally only become active after the actual construction process can already be used during the printing process. This includes, for example, the following activities:
- Inserting air layer anchors for the insulation level
- Pulling the ducts and covering them with insulation
- Placing electrical installation boxes
By way of comparison, it normally takes four to five people about a week to complete one storey. 3D house printing, on the other hand, requires two people to operate and about 20 hours of printing time to complete one storey.
Cost factor
Because of the high printing speed, 3D construction is cheaper than a conventionally built house. This is because fewer workers are needed to oversee the construction. The material costs are slightly lower than conventional construction because efficient planning of resources is carried out in advance and less waste is produced during the printing process. However, the costs for technical equipment are higher than for conventional wall construction. Overall, 3D printing house costs are currently about 25% – 30% lower compared to conventional construction.
Safety
Another difference between 3D printed houses and those built conventionally is worker safety. Workers in the construction industry are usually exposed to increased safety risks, injuries, and occupational diseases such as herniated discs are common among construction workers. When building a house with a 3D printer, there is a lower risk of occupational accident or injury caused by heavy physical work. This in turn also reduces costs, as the employer incurs fewer expenses for insurance and sick pay.
The 3D printing construction process is not only suitable for building houses. Other objects and structures can also be produced with the technology, for example, fireplaces, bridges, or unusual architectural designs, which until now could only be produced in very complex and therefore costly ways.
What processes are available to produce 3D printed homes?
There are a variety of different processes and materials used in the 3D printer construction process. The printers, which can be of different sizes, visually resemble a crane and are mostly installed at the location where the house is to be created. However, printing can also take place at another production site. Then, after the material has hardened, the individual elements are transported to the place of construction and assembled there. One factor common to all processes is that the printer applies the material layer by layer in slow rotating movements. Some of the common 3D house printing methods can be seen below:
Extrusion process
The extrusion process or fused layer modelling is currently the most widespread method used to make concrete 3D printer houses. A special concrete is used for this, which has different properties than conventional concrete and therefore enables a completely different method of working.
Extrusion Process | Properties |
---|---|
Features | • Formwork-free construction • Layer-by-layer, three-dimensional construction • No geometric edges and shapes, rounded design |
Advantages | • The process is characterised by its speed • Cost-effective • Breakthroughs or changes in density properties possible at any time |
Weak points | • The individual layers must be pressed together in order to adhere to each other • This can lead to difficulties with the bending tensile strength |
Selective binding
Selective binding is distinguished by two sub-processes:
Process | Characteristics |
---|---|
Wet printing / paste intrusion | • Different components are applied in layers on top of each other, e.g. sandstone on cement paste • A good bond between the elements must be ensured in order to achieve high stability |
Selektive Aktivierung | • Layer-by-layer application of cement-sand mixture • Water is sprayed on where the material is to consolidate (also layer by layer) • Excess material is removed and used for a new print structure (removal e.g. with the help of a suction cup) |
With these methods, complex geometric elements can be produced, thus even unusual architectural ideas can be realised. As the unbound dry material has a high supporting effect, selective binding can be used to produce simple structures with cavities. However, the process is more cost-intensive than the extrusion process. In addition, it is currently not conclusively clarified how it reacts to different weather conditions.
Examples of 3D printing construction
Buildings have already been printed in various projects around the world. In Calverton, New York, a single-family house measuring approximately 177 square metres was built in only eight days. The 3D printer required 48 hours of pure printing time, and the material costs amounted to less than 6,000 dollars. By comparison, even prefabricated houses normally take several months to build.
In 2020, the first German 3D printed house was built in Beckum, North Rhine-Westphalia. It was a two-storey single-family house with about 160 square metres of living space. Only sustainable materials were used as insulating materials. Since there are currently no uniform guidelines for the approval process, the North Rhine-Westphalian building authority granted the pilot project a building permit on a case-by-case basis. In addition, the project was subsidised with 200,000 euros in funding.
Can 3D printed houses be built sustainably?
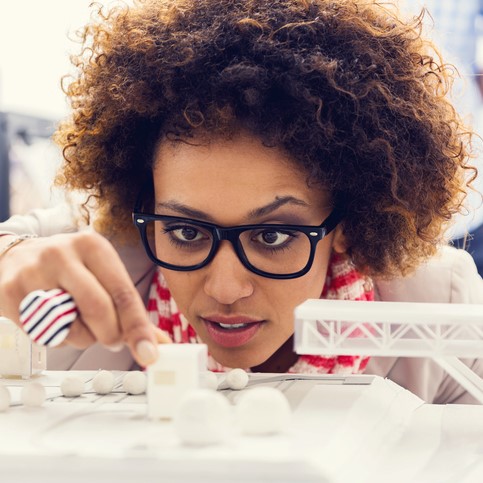
Concrete is not necessarily one of the most sustainable materials, as its production releases an enormous amount of CO2. Nevertheless, the 3D construction process is far more efficient and produces less material waste than conventional house construction. The pilot project in Beckum shows that through the selection of components, materials, and the efficient construction method, up to 50% of CO2 can be saved compared to conventional construction.
A house built with the 3D printer is particularly sustainable if resource-conserving materials such as wood or dirt are used instead of concrete, glass, or plastic. The Italian company WASP demonstrated with its ‘Tecla’ project, showing that a building can be printed exclusively from locally available resources. In the Italian city of Ravenna, the prototype of a house was built from 60 cubic metres of earth in 200 hours of printing – without the use of any other materials.
Challenges of 3D printing construction in urban planning
3D printed homes have many advantages but there are challenges too. Let’s take a closer look at some of the issues facing 3D printing technology:
- Dealing with expertise: Architects have greater freedom to implement more complex designs with 3D printed homes than with conventional construction. However, they also face a special challenge because these new materials have different properties and load-bearing capacity compared to conventional concrete. This makes the work for architects and builders more complex than in the past and means they must acquire knowledge of the new materials
- Scepticism in the industry: Interdisciplinary teamwork is already required in the planning phase, as decisions must be made early and all trades have to be coordinated. Currently, there is still a certain scepticism in the construction industry regarding the use of the technology and the associated handling of new data. However, as soon as 3D printing technology becomes more widely used in urban planning, it will also become more established in the construction industry
- Current legal situation in the UK: The legal situation regarding 3D printing technology for the construction of buildings is currently not uniformly regulated, as there are still no standardised approval procedures. The greatest challenge for the industry at present is therefore to establish norms and standards that make it easier for the building supervisory authorities to issue permissions. However, these will surely come in time as the technology becomes more widely used
What impact could 3D printing technology have on the construction industry?
Provided that the technology becomes more established, it could signal widespread changes in the construction and real estate industries, as well as in environmental protection and society as a whole. 3D printed homes have the potential to lead the way for the emergence of new job profiles. The way buildings are created and how work is done on construction sites could also fundamentally change. Time consuming construction projects with large workforces could soon be a thing of the past. The industry could also change in the following ways:
- House printing will be controlled and monitored from a laptop. This makes the construction industry attractive for the younger and more technologically minded generation. Whereas strength and physical resilience were previously important prerequisites for working on a construction site, technical understanding and a high level of professional expertise are paramount when it comes to 3D printed homes. New job profiles in the field of engineering and architecture are emerging, and the risk of injury during construction is decreasing. This also makes jobs in the construction industry more attractive for upcoming generations
- Housing can be built faster and cheaper
- Affordable housing created in this way could contribute to more equity in the housing market
- Even unusual forms and designs in urban development are no longer necessarily associated with high costs, but can be created quickly and comparatively cheaply
- The sustainability of the construction method saves resources and reduces CO2 emissions
FAQ for 3D printing houses
In the planning phase, 3D objects are first developed with CAD software. The data is translated into an STL format and transferred to the 3D printer, ready for production. The printer can be set up on site, it applies the material layer by layer and can produce even complex architectural shapes.
For 3D printing house construction, the most common material used is a specially developed concrete that consists of sand, cement, water, and other ingredients. The special concrete can be mixed with various additives such as plastics (thermoplastics, elastomers), precious metals (titanium, stainless steel, tool steel, alloys), wood and fibres. These support the material with their respective strengthening properties. The use of resource-saving materials is also currently being researched and is in constant development.
The material must have completely different properties than conventional concrete:
• It needs to set quickly and be dimensionally stable so that the subsequent layer can be applied quickly
• At the same time, the material must be pliable enough so that the top layer can bond with the bottom layer to create a stable wall
• The concrete must not clog the nozzle on the printer head
• The material must be adapted to the respective printer model so that everything works smoothly
The 3D printing process could be used in the future to create housing quickly and inexpensively, meaning the housing shortage in the UK could be reduced. An application in social housing could give lower-income households affordable housing options and even reduce homelessness. Architects will be able to use the technology to realise innovative designs and unusual constructions, thereby changing the conventional cityscape.
Standards for requirements in the 3D house printing industry must still be established. Scepticism still prevails in the building industry, and the necessary expertise must be developed in many areas. In addition, the technology is constantly being developed, and research into materials and processes is dynamic, which can have drawbacks
Image source:
© gettyimages.de – Yuri_Arcus, Jirakojpraditcharoenkul, Izusek