Table of contents
In general, hydraulics is a technology that uses liquids to generate pressure and convert it into mechanical energy. Hydraulic cylinders and pumps make it possible to lift heavy loads with minimal effort. They are also used in couplings or braking systems of commercial vehicles. This guide explains what hydraulic power is, the physical processes involved, and how the power transmission is practically implemented.
What is hydraulics?
The word hydraulics is derived from two Greek words: “hydro” meaning water or liquid, and “aulos” meaning pipe or conduit. Together, these words indicate what makes up a hydraulic system: a liquid is introduced into a closed system where mechanical or static force creates or increases pressure. The power generated by hydraulic systems is many times greater than the original force applied.
Here is where there is a significant difference between hydraulics and pneumatics: while hydraulic systems use liquids to create the necessary pressure, pneumatic systems rely on gases.
In both methods, the created pressure is transmitted through hoses or piping until it triggers the desired mechanical reaction at a specific point. In this way, large forces can be generated with relatively low energy consumption, making it possible to lift heavy loads, drive machines, or move certain components.
In which areas is hydraulics used?
Due to their advantageous properties, hydraulic components are used in a wide range of work areas. These include, for example:
- Agriculture and construction machinery: attachments for excavators, cranes, tractors, as well as bucket and tipping functions
- Workshop: hoists, tools, machine lifters
- Automotive technology: clutch, brakes, power steering, suspension
- Material handling: forklifts, hand pallet trucks
- Elevator technology
- Production: hydraulic presses, test bench technology, conveyor belts
Suitable hydraulic fluids
Hydraulic systems typically operate using a specialized oil (hydraulic oil) instead of water. This oil is ideal for ensuring gentle operation within the precision mechanics of machines and engines due to its properties. However, other liquids and mixtures can also be used as hydraulic fluids if they possess specific characteristics including:
- viscous and lubricating
- wetting and adhesive
- resistant to aging
- acid-free
- foam-free
- low compressibility (the volume should not decrease under pressure)
Depending on the application, hydraulic oils may be composed of mineral oils, vegetable oils, water-oil emulsions, or synthetic fluids. Further properties, such as corrosion protection or food compatibility, can be achieved through different additives and compositions.
Hydraulic system components
Hydraulic systems can move large loads with a manageable amount of force. Various hydraulic fittings and components play a role in this process within the system. The most important ones are:
- Power source: used to operate the hydraulic pump, either manually or through a motor.
- Hydraulic fluid: the liquid within the system.
- Hydraulic pump: generates pressure by displacing the fluid.
- Hydraulic hoses and pipes: transport the hydraulic fluid through the system.
- Valves: regulate the amount of fluid (and therefore pressure) in different areas of the system.
- Hydraulic cylinders or motors: convert the pressure into mechanical energy.
- Pressure gauge: displays the pressure within the system.
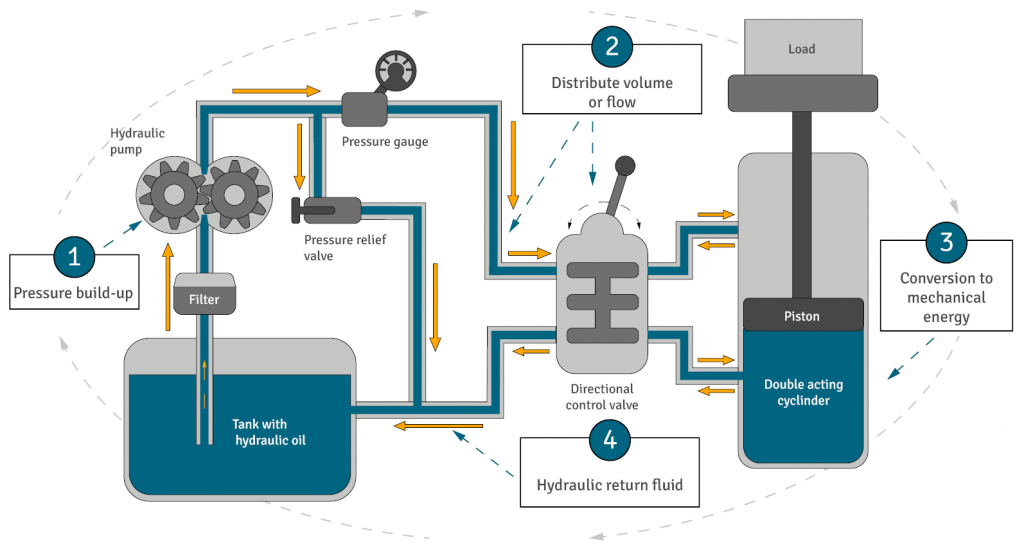
How do hydraulics work?
- Building up pressure
The hydraulic pump is operated either manually (for example, by operating a lever or pedal) or with a motor. By moving the piston, the space for hydraulic oil is reduced. The pressure continues to increase.
- Distributing volume or flow rate
The fluid under hydraulic pressure is also known as the volume or flow rate. It is distributed through the hydraulic pipes in the system. In complex systems, valves can be used to control the direction of the flow rate.
- Conversion into mechanical energy
Once the fluid has spread through the pipes and built up sufficient pressure, it triggers a second hydraulic cylinder or motor that is responsible for the corresponding process (such as lifting a lift or activating the brakes).
- Returning the hydraulic fluid
In spring-supported manual systems (such as a brake system), you simply need to let the lever glide back to its starting position to reduce the pressure again. For larger construction machines or powerful hydraulic stacker trucks, there is usually a second switch that lowers the piston and opens a return valve, allowing the hydraulic oil to be evenly distributed again in the system.
The advantages of hydraulics
Although the functionality is very similar, there are several advantages that hydraulic systems have over pneumatic systems. Hydraulic systems and drives are extremely powerful. Compared to other drives, they can be installed in a space-saving manner, move or absorb large loads, and are very low-wear even under the highest loads, thanks to the oil.
All the advantages of hydraulics at a glance:
- High power transmission
- Relatively low space requirement
- Good adaptation to spatial conditions thanks to flexible hoses and pipes
- Suitable for precision machinery due to slow and individually adjustable movements
- Durable and low-wear (with proper maintenance and use)
- Hydraulic oil prevents friction and serves as a coolant, increasing the service life of the system.
FAQ for hydraulics
The term “hydraulics” is derived from two Greek words: “hydro” meaning water or fluid, and “aulos” meaning pipe or conduit. From this, it can already be deduced what constitutes a hydraulic system: a fluid is introduced into a closed system where pressure is subsequently built up through mechanical or static means. This pressure is then transmitted through hoses or pipes until it triggers the desired (mechanical) reaction at a specific location. In this way, large forces can be generated with relatively low energy input, which can be used for lifting loads, driving machines, or moving specific components.
Despite having similar functions, hydraulic and pneumatic systems are fundamentally different. Pneumatic systems use gases instead of liquids to generate the necessary pressure.
• Land and construction machinery: attachments for excavators, cranes, tractors, as well as bucket and tilting functions
• Workshop: lifting platforms, tools, machine lifts
• Automotive engineering: clutch, brakes, power steering, suspension
• Storage technology: forklifts, hand pallet trucks
• Elevator technology
• Production: hydraulic presses, testing equipment, conveyor belts
• High power transmission
• Relatively small space requirement
• Good adaptation to spatial conditions thanks to flexible hoses and pipelines
• Suitable for precision machines due to slow and individually adjustable movement sequences
• Durable and wear-resistant (with proper maintenance and use)
• Hydraulic oil prevents friction and serves as a coolant, thereby increasing the service life of the system
Image source:
© Jungheinrich AG